Understanding the Essentials and Applications of Plastic Extrusion in Modern Production
In the realm of contemporary production, the strategy of plastic extrusion plays an instrumental duty. Untangling the principles of this process exposes the real convenience and potential of plastic extrusion.
The Basics of Plastic Extrusion Refine
While it may show up complicated, the basics of the plastic extrusion process are based on reasonably straightforward principles. It is a production procedure where plastic is thawed and then shaped into a continual account through a die. The plastic extrusion procedure is thoroughly used in various industries due to its convenience, effectiveness, and cost-effectiveness.
Different Kinds Of Plastic Extrusion Techniques
Structure upon the basic understanding of the plastic extrusion procedure, it is required to discover the various methods associated with this production approach. Both main strategies are profile extrusion and sheet extrusion. In profile extrusion, plastic is thawed and formed into a continual account, typically used to produce pipelines, rods, rails, and window frameworks. On the other hand, sheet extrusion creates big, level sheets of plastic, which are normally further refined into items such as food packaging, shower curtains, and auto parts. Each technique needs specialized equipment and specific control over temperature level and pressure to make sure the plastic keeps its form during cooling. Understanding these strategies is key to utilizing plastic extrusion successfully in contemporary production.
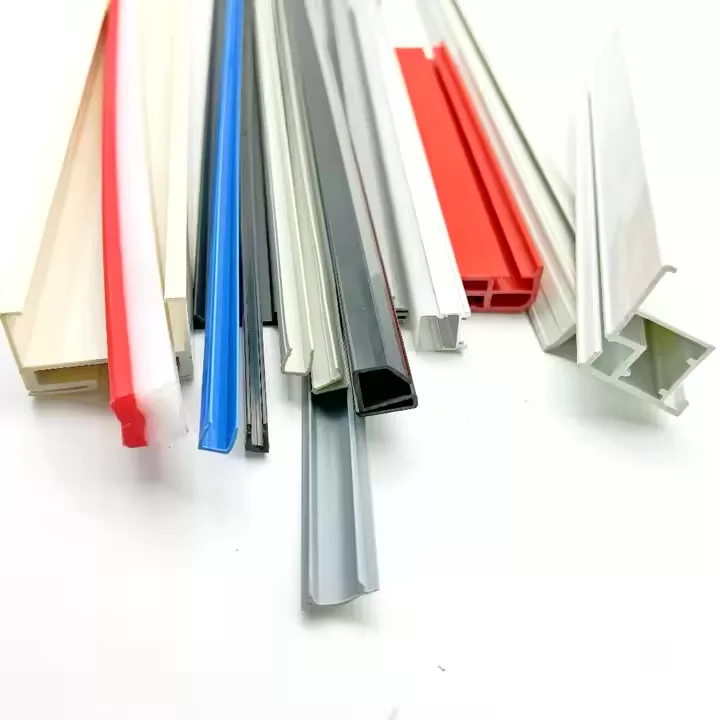
The Duty of Plastic Extrusion in the Automotive Sector
An overwhelming majority of parts in contemporary vehicles are items of the plastic extrusion process. This procedure has transformed the automobile market, changing it into an extra efficient, economical, and adaptable manufacturing industry. Plastic extrusion is primarily made use of in the production of various auto elements such as bumpers, grills, door panels, and dashboard trim. The process gives an uniform, consistent directory output, allowing manufacturers to generate high-volume parts with excellent precision and very little waste. The lightness of the extruded plastic components adds to the overall decrease in vehicle weight, boosting gas effectiveness. Additionally, the durability and resistance of these parts to warmth, cold, and effect improve the Look At This longevity of cars. Thus, plastic extrusion plays a pivotal function in auto manufacturing.

Applications of Plastic Extrusion in Durable Goods Production
Beyond its significant impact on the vehicle market, plastic extrusion confirms just as efficient in the realm of customer goods producing. The adaptability of plastic extrusion allows suppliers to develop and create complicated forms and sizes with high precision and effectiveness. The versatility, adaptability, and cost-effectiveness of plastic extrusion make it a recommended option for several consumer goods manufacturers, contributing substantially to the sector's growth and technology.
Environmental Impact and Sustainability in Plastic Extrusion
The prevalent use of plastic extrusion in making welcomes examination of its eco-friendly effects. Reliable equipment minimizes power usage, while waste monitoring systems reuse scrap plastic, lowering raw material needs. In spite of these improvements, additionally advancement is required to minimize the ecological footprint of plastic extrusion.
Conclusion
In conclusion, plastic extrusion plays a vital duty in modern-day manufacturing, particularly in the vehicle and customer items sectors. Its versatility permits the click to read production of a vast array of components with high accuracy. Moreover, its possibility for reusing and development of naturally degradable products uses a promising method in the direction of lasting methods, thus attending to ecological concerns. Recognizing the basics of this process is key to enhancing its benefits and applications.

The plastic extrusion procedure is extensively utilized in numerous industries due to its convenience, effectiveness, and cost-effectiveness.
Building upon the basic understanding of the plastic extrusion process, it is essential to explore the various strategies involved in this manufacturing approach. plastic extrusion. In contrast, sheet extrusion develops huge, level sheets of plastic, which are typically more refined right into products such as food product packaging, shower drapes, and cars and truck components.An overwhelming majority of components in contemporary vehicles are items of the plastic extrusion procedure